Roll Grinder Technology that Creates Added Value
Customized Solutions With a Vision of the Future
Roll grinding machines are designed for decades of operation. Regular inspections and continuous service activities are essential to ensure high precision, availability and efficiency in the production process in the long term.
As an established maintenance partner, we offer a comprehensive and clearly structured range of services to sustainably increase profitability in roll processing.
Linear Guide Technology
High Stability and Dynamics in the Grinding Process
With the direct infeed concept, the roll grinding geometry is produced directly by the grinding head (X-axis) without an additional superimposed axis. High-precision and generously dimensioned linear guides in combination with absolute position monitoring ensure backlash-free axis movements without a stick-slip effect. This guideway system means that the grinding head can be designed as a one-piece composite structure with a mineral cast body and guarantees maximum rigidity, optimum dynamic system behavior and thermal insensitivity.
- Perfect for roughing and finishing: Optimum load rigidity enables high forces to be used without any loss of accuracy or resonance frequencies
- High electronic axis resolution ensures outstanding dynamics with perfect positioning accuracy.
- Best machine availability and long-term accuracy thanks to generously dimensioned linear guides.
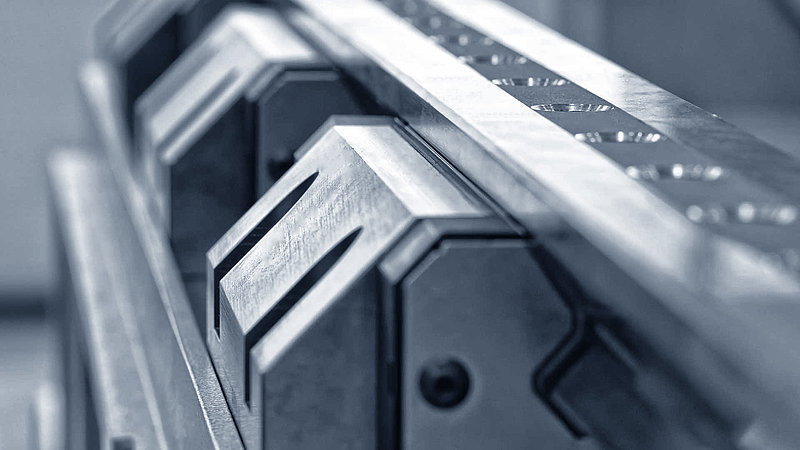
Motor Spindles
Innovative Motor Spindles for the Highest Possible Precision
The wheel spindle is the central element of every grinding machine. It is the key component for machine performance and surface quality. Our sba motor spindles combine innovative technology with maximum precision and performance.
- Backlash-free direct drive of the wheel spindle - Free from vibrations, imbalance, slip and belt tension
- Maximum system rigidity thanks to the elimination of long drive trains
- Better control dynamics thanks to the direct connection of the grinding wheel
- Flexibility through application-specific selection of drive power and bearing principle (hydrodynamic or hydrostatic)
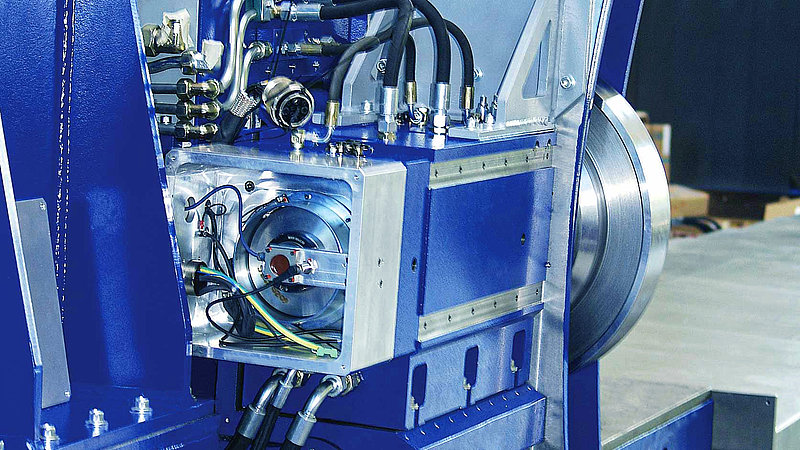
Roll Grinder Control
KP10
Pioneering in Performance and user-Friendliness
The pioneering KP 10 grinding machine control system sets new standards in terms of performance potential and user-friendliness. The latest version is a PC-based real-time control with Windows operating system, in which all of the complex processes of roll handling, machining and inspection are integrated. The intuitive operability combined with the powerful system architecture makes the grinding process faster, more flexible and more efficient than any other system currently available, even for the most demanding roll grinding geometries.
- As simple and safe to operate as a smartphone - and just as easy to learn
- Transparent grinding process: Measurements and input parameters are saved in chronological order and can be called up at any time
- High-performance architecture is based on standard industrial components and guarantees high availability systems
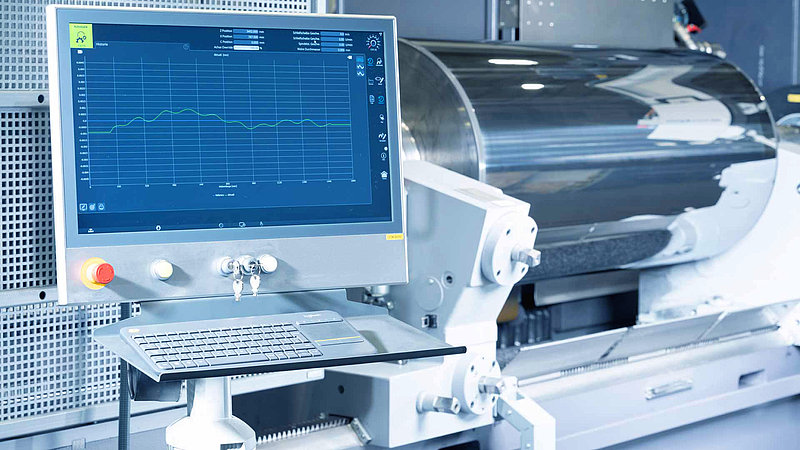
C-Frame-Technology
Maximum Efficiency and Rolls Ground with High Precision
The C-frame calipers from the HerkulesGroup are high-precision measuring systems for measuring the geometry of rolls. Thanks to their compact and stable design, the measuring devices can be used flexibly and are therefore suitable for all roll types. The advantage: Maximum cost efficiency in the grinding process. Reduction of stock removal on the roll barrel to a bare minimum.
- Absolute measurements - no interpolation based on a single measuring point for high-precision grinding results
- Significant productivity gains through real-time corrections “on the fly”
- 3-point measurement of the roll position using the C-frame and 3rd measuring probe on the grinding wheel side
- As much as necessary, as little as possible
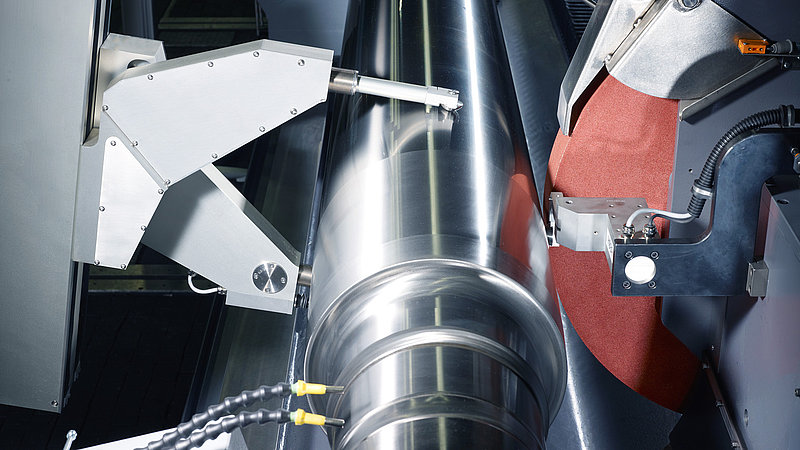
Roll Inspection – Eddy Current & Ultrasound
Early Detection of Roll Defects
To ensure the profitable operation of rolling mills, roll defects must be seamlessly detected and eliminated.
The high-resolution Eddy Current and Ultrasonic inspection systems reliably localize manufacturing and fatigue defects near the roll surface and inside the roll.
- Eddy current testing to localize open cracks and structural changes on the roll surface
- Ultrasonic testing to detect casting defects and evaluate the bonding quality between the roll shell and core
- Diagnosis in real-time measurements “on the fly” during the grinding process
- Complete integration into the grinding machine control system or as a stand-alone system
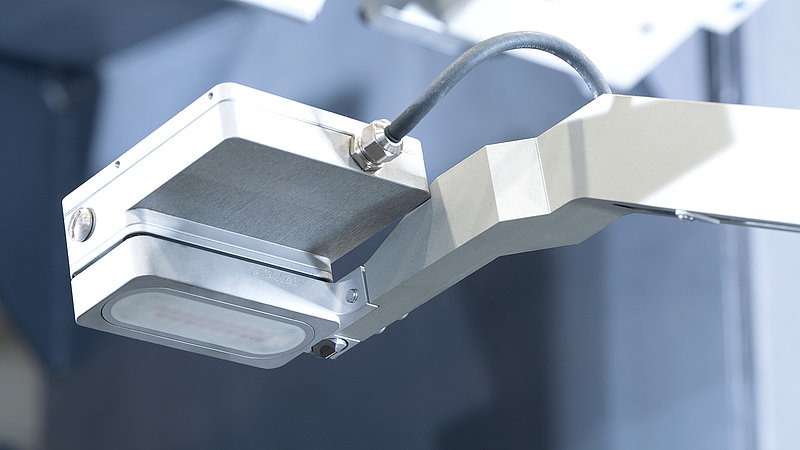
Surface Inspection - Roll Surface Inspection System RSIS
Reliable Inspection of the Roll Surface
sba offers the Roll Surface Inspection System RSIS laser measuring device for the automated detection of optical defects on the roll surface. In the post-process, the RSIS detects and analyzes the reflection of a laser beam on the roll surface. Machining defects such as chatter and feed marks, commas, clouds, and similar defects are thus reliably identified.
- Detects all types of optical defects on the roll surface
- Objective quality control regardless of the operator's experience
- Ensures repeatability and uniformity of the surface quality
- Fully integrated into the grinding machine control system or as a stand-alone system
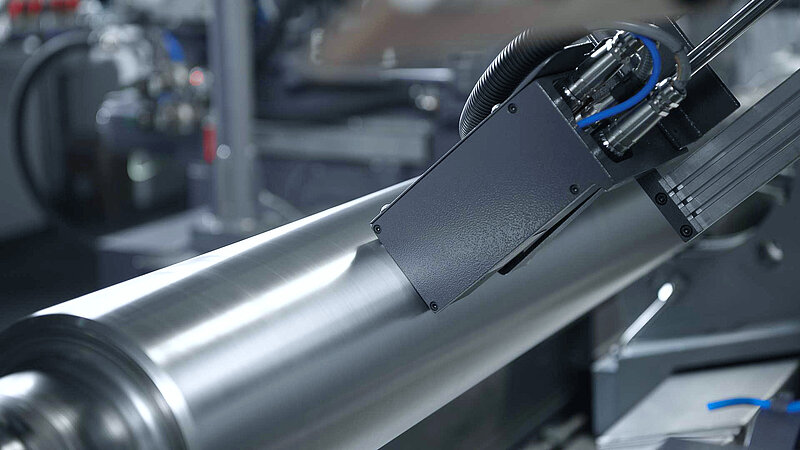
Roughness Scattered Light Detection RSLD
Optical Measuring Method for Extremely Sensitive Surfaces
The specific functional properties of flat products for certain industries require perfect homogeneity of the roll surface in the rolling process. The Roughness Scattered Light Detection RSLD measuring technology, which determines and documents the surface roughness over the entire roll barrel area without contact by means of scattered light, offers the ideal solution for ensuring optimum production conditions.
- Non-contact and non-reactive inspection of the entire roll surface
- Real-time diagnostics - measurements “on the fly” during the grinding process
- Analysis of the functional surface properties (e.g., friction behavior and load-bearing capacity) of the roll
- Output of the scattered light diffusion value (Aq) - equivalent conversion to the surface roughness value (Ra)Output of the scattered light diffusion value (Aq) - equivalent conversion to the surface roughness value (Ra)
- Measurements in the grinding and rolling direction
- Complete integration into the grinding machine control system or as a stand-alone system
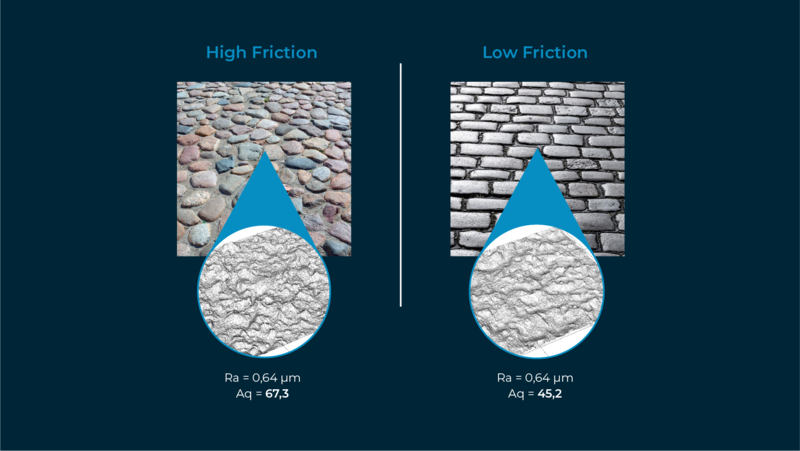